Un equipo de científicos de la Universidad de Jaén y del Instituto de Ciencia de Materiales de Sevilla (CSIC y Universidad de Sevilla) ha desarrollado una espuma rígida con polvo procedente de la industria del aluminio y cenizas de cáscara de arroz. Este material puede emplearse en una amplia variedad de sectores como la construcción, la aeronáutica y el diseño de interiores.
Un equipo de investigación de la Universidad de Jaén y del Instituto de Ciencia de Materiales de Sevilla (centro mixto del CSIC y la Universidad de Sevilla en el Parque Tecnológico de La Cartuja) ha patentado una espuma rígida porosa fabricada con residuos y menos contaminante que el cemento tradicional. En concreto, los expertos proponen una técnica que emplea polvo de filtro de la industria del aluminio y cenizas de cáscara de arroz para crear un ‘cemento’ con una dureza y resistencia similares a la madera, que además posee cualidades como aislante térmico y acústico.
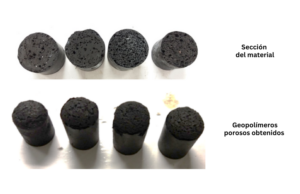
La espuma geopolimérica puede emplearse en campos como la industria aeronáutica, aeroespacial y en la construcción.
Las espumas geopoliméricas se forman con cenizas de cáscara de arroz y polvo de filtro de la industria de aluminio. Para elaborarlas, se combinan a temperatura próximas a la ambiente mediante un proceso químico de reacción y, de este modo, se genera la espumación y se forman los poros. Se trata de un proceso muy similar al que sufre la masa de un bizcocho cuando se hornea y se llena de huecos. “No obstante, al contrario que este dulce, que suele quedar esponjoso y blando, el material propuesto por los expertos presenta una solidez similar a la del cemento y cualidades como aislante térmico y acústico, entre otras.
Espuma porosa
Tal y como explican los investigadores en la patente ‘Utilización de polvo residual de la industria del aluminio para la obtención de espumas rígidas geopoliméricas, material obtenido y usos del mismo’, para fabricar el cemento geopolimérico son necesarios dos ingredientes. Por un lado, un material sólido de origen mineral silicoaluminoso (precursor); por otro lado, una solución que active al primer material. De este modo, se forman los compuestos químicos que aportan resistencia y solidez.
Los expertos indican que como precursores se pueden utilizar materias primas naturales, como el caolín u otras arcillas, o fuentes residuales como las escorias metalúrgicas, las cenizas la combustión de carbón y biomasa, residuos de construcción y demolición e incluso lodos de depuración de aguas residuales, entre otros. Estos cementos ligeros, al elaborarse a temperaturas próximas a la ambiente, se presentan como una alternativa menos contaminante. “Con la técnica que proponemos aportamos la posibilidad de generar una espuma rígida con numerosas aplicaciones y con todas las ventajas de la producción de los materiales geopoliméricos”, explica a la Fundación Descubre la investigadora de la Universidad de Jaén Dolores Eliche.
Para elaborar este material, los investigadores mezclaron el polvo de filtro de la industria de aluminio y cenizas de cáscara de arroz. A continuación, añadieron como activador una solución de hidróxido sódico (sosa cáustica) y una sustancia química llamada silicato sódico. Con esta combinación, crearon un medio muy alcalino. Esto es, como si mezclaran la harina, la levadura y los ingredientes sólidos de un bizcocho con la leche.
Alternativa sostenible
Una vez producida la reacción de geopolimerización y espumación, la mezcla obtenida se introdujo en moldes a una temperatura de entre 40 y 60 grados centígrados durante un día para que se endureciera. Al día siguiente, los investigadores desmoldaron el producto y lo dejaron a una temperatura ambiente para someterlo a ensayos físicos, mecánicos (para comprobar cuestiones como su dureza y resistencia) y térmicos. De este modo, mediante el aprovechamiento de residuos o subproductos industriales y una reducción de la temperatura durante el proceso de fabricación, los expertos minimizaron la emisión de dióxido de carbono, contaminante para la atmósfera. “Hemos determinado que la huella de carbono que genera su elaboración es baja, y además, le damos una nueva utilidad a los residuos de la industria agrícola y de la metalurgia del aluminio, que con frecuencia se depositan en vertederos. Así, contribuimos a una economía circular y sostenible”, comenta Dolores Eliche.
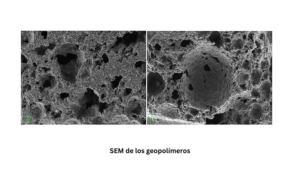
Detalle del material final: un ‘cemento’ ligero con la dureza y resistencia similares a la madera.
Los investigadores del grupo Ingeniería Química y Ambiental de la Universidad de Jaén indican que la patente está en fase de laboratorio y para su empleo a mayor escala habría que someter el material a más estudios preliminares con empresas para comprobar la extensión de sus propiedades catalíticas, aislantes y depuradoras. No obstante, Dolores Eliche señala: “Si superase estas pruebas, se trataría de una alternativa muy económica para los empresarios y más sostenible que se puede emplear en varios sectores, incluido el de la construcción.
Este proyecto ha sido financiado por la Universidad de Jaén, patrocinado por Caja Rural de Jaén para el proyecto ‘Valorización de distintos tipos de ceniza para la obtención de distintos materiales cerámicos sostenibles’.
Compartir: